As spring approaches Valley Center, homeowners often start thinking about the reliability of their sump pumps. These systems play an essential role in preventing basement flooding by directing water away from foundations. Yet, their efficiency heavily depends on a small component: the float switch. This piece is crucial in determining when the pump should activate and deactivate in response to water levels. Any malfunction in the float switch can disrupt this vital process, leaving homes vulnerable to water damage.Understanding the issues related to sump pump float switches helps homeowners maintain peace of mind and a dry basement environment throughout the year. Recognizing the significance of this small component can prevent major headaches during heavy rains. Let’s explore what a sump pump float switch is and why it is such an important part of the system.
What Is a Sump Pump Float Switch?
A sump pump float switch is a device that detects the water level in a sump basin. It is designed to activate the sump pump motor when water reaches a certain height, triggering the pump to remove excess water from the area. As water subsides and reaches a lower threshold, the switch turns the pump off, conserving energy and preventing dry runs.Inside the sump pump system, the float switch plays the role of an automated controller, responding to changes in the water level. Depending on the setup, this switch can be tethered, vertical, or electronic, each with unique mechanisms for sensing water levels. Imagine a float in a child's toy boat; as the water rises, the float lifts, signaling the need for action—in this case, the action being the activation of the pump to prevent flooding.The proper functioning of the float switch ensures that water does not linger in the basement, avoiding potential water damage or mold growth. When installed and maintained correctly, this switch enables your sump pump to protect your home effectively, especially during the rainy season.
Common Float Switch Problems
Float switches, like any mechanical component, are subject to wear and tear over time. Recognizing potential problems early can prevent more extensive damage. Here are some common issues associated with sump pump float switches:
1. Sticking or Jamming: Debris or dirt accumulation in the sump pit often causes the switch to stick or jam, preventing it from moving freely. When a switch gets stuck, the pump might fail to start, leaving water unchecked.
2. Electrical Malfunctions: Faulty wiring or defective parts can lead to electrical failures, preventing the pump from activating when necessary. These issues might require attention from our technicians to ensure safety and functionality.
3. Wear and Tear: Like any moving component, the float switch may degrade over time due to frequent use. This wear can disrupt its ability to properly sense water levels, risking potential overflows.Identifying the signs of float switch problems often involves observing the sump pump's behavior.
If the pump fails to turn on when the basin fills, or if it runs without stopping, these symptoms may indicate switch-related issues. Addressing these problems promptly not only protects your basement but also extends the life of your sump pump system.
Troubleshooting Float Switch Issues
Addressing issues with your sump pump float switch is essential to prevent water damage in your home. Knowing how to diagnose and fix common problems allows you to act quickly. Start by observing your sump pump's behavior. If the pump doesn't turn on or off correctly, the float switch could be the culprit. Here are some steps to help identify and manage these issues:
- Ensure the Power Supply: Before diving into fixes, always check if the sump pump has power. Sometimes the problem is as simple as a disconnected plug or a tripped circuit breaker.
- Inspect for Debris: Remove any debris caught in the sump pit. Dirt or objects can block the float switch, preventing it from moving. Clean the pit regularly to avoid such issues.
- Test the Float Switch: Lift the float manually to see if the pump activates. If the pump works manually but not automatically, the switch may need replacement.
- Check for Wear and Damage: Look for any visible signs of wear or damage. Over time, the components can degrade, affecting performance, and replacing these might be necessary.
- Listen for Strange Noises: Unusual sounds can indicate a mechanical issue with the switch or pump motor. Our professionals can help diagnose deeper mechanical or electrical problems to ensure safe operation.
Safety is paramount when dealing with electrical equipment. Always proceed with caution and consult our technicians for a thorough inspection and any complex fixes. Resetting the float switch could provide a temporary solution in minor cases, but full replacement ensures reliability.
Preventive Maintenance Tips
Keeping your sump pump's float switch in good shape reduces the frequency of problems and ensures a longer lifespan for your system. Regular maintenance is crucial, especially in Valley Center, where spring rains can be heavy. Consider these key maintenance tips:
- Conduct Routine Inspections: Regularly check the sump pit and the condition of the float switch. Early detection of issues can prevent emergencies.
- Schedule Seasonal Cleanings: Clean the sump pit before the rainy season to remove accumulated sludge and debris. It helps the float move freely and work effectively.
- Watch the Weather: When heavy rain is forecasted, check your system's responsiveness. Being proactive before a downpour can avert disaster.
- Professional Inspections: Regular inspections by our technicians ensure your system is operating at its best. They can spot and handle issues that might be missed during casual checks.
Ensuring Your Sump Pump is Ready Year-Round
In Valley Center, keeping your sump pump ready for action regardless of the season is key to protecting your home. Regular upkeep helps prevent float switch problems and ensures your basement stays dry. Proactive measures, such as routine checks and periodic cleaning, extend the functionality of your system.A reliable sump pump not only shields your home from immediate water threats but also protects it from potential long-term structural damage. Engaging in consistent maintenance and timely inspections is a small effort for the peace of mind it provides. Taking these steps helps make sure your sump pump operates effectively throughout the year, offering lasting protection against the elements.Keep your home safe with reliable maintenance that protects your sump pumps in Valley Center and prevents basement flooding during heavy spring rains. If you need support or routine service to ensure your system stays in top shape, our professionals can help; for a quick estimate or to book a service visit, please contact us today.
Customer Testimonials
Hear from satisfied customers who trust us for reliable HVAC and plumbing service across Wichita.
Plus, the technician, Lee was very professional, knowledgeable and informative.
We will definitely be doing business with them sometime again in the past.
I'm prompt to my appointment. Thank you Midwest Mechanical.
Financing
For your convenience, we work with a variety of lenders in offering a large selection of flexible financing options with approved credit.
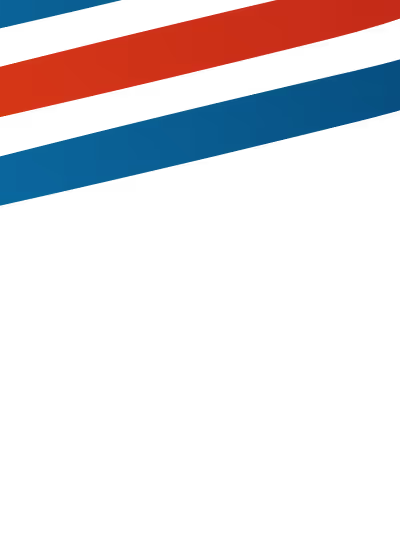